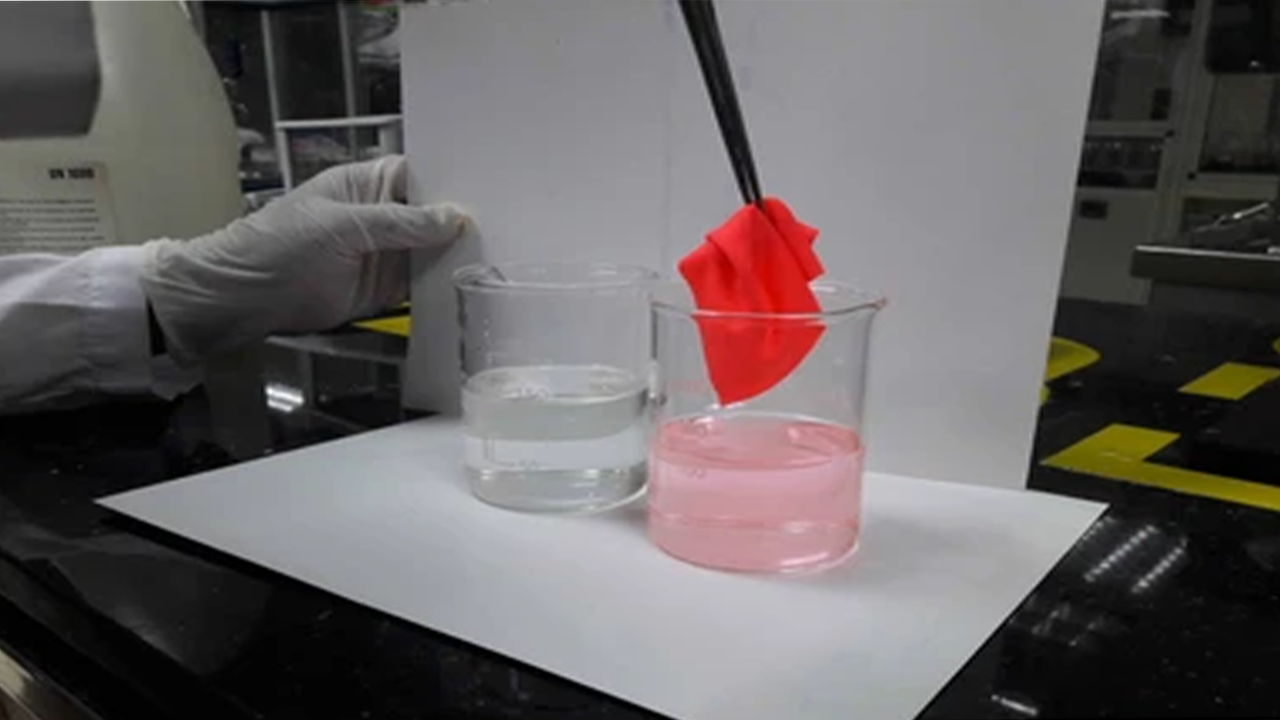
Engineered fabrics
The current popularity of engineered fabrics is not recent; instead, it is the result of a protracted transition from triple-layer fabrics to three-dimensional materials. Engineered fabrics are now essential since their range of uses has expanded from the automotive industry to aerospace, the marine industry to geo-engineering, sporting goods to packaging materials, etc. Additionally, solution-focused and custom-designed fabrics are included in engineered fabrics. These goods are also used in nonwoven, corrugators, building products, tanneries, and textile industries, which are process industries unrelated to papermaking.
Suitable raw material for engineered fabrics
Many different natural fibers have the potential to be used in engineered fabrics. Cotton, flax, jute, and sisal are the primary natural fibers used as the foundation for engineered fabrics. These fibers are utilized to create a variety of heavily engineered fabrics, including ropes, belts, needle-punched nonwoven fabrics for geo applications, and canvas. However, various restrictions on these fibers prevented their use in engineered fabrics, notable for their increased stiffness, susceptibility to microbial and fungal attacks, poor water resistance, and lower flame retardancy. Jute is a readily available, inexpensive fiber used in treated and gray forms in engineered fabrics. Manufacturing of ropes, nets and twines can be done with sisal fiber.
Three-dimensional woven engineered fabrics
To improve woven engineered fabrics’ strength, thickness, extensibility, porosity, and durability, three-dimensional woven engineered fabrics are created.
By adjusting the weave, thread spacing, raw material structure (filament or staple), linear density (or count), and twist factors of the warp and weft yarns, it is possible to design the performance of 3D woven fabrics. The creation of engineered materials with the appropriate qualities possible innumerably by 3D woven fabrics.