There are numerous famous and widely utilized yarn formation systems. Some of them are filament yarn formation technologies for worsted or cotton wool. This page also discusses some of the more popular forms of yarn, such as mercerized, colored, grindle, and twisted yarns.
Professional Experience.
Dyed Yarn
The strands that have been dyed are used to create fabrics with stripes and jacquard patterns. Both sophisticated equipment and hand labor are used to color yarns. We cannot anticipate shade consistency, yarn strength, or higher quality when dyeing yarn by hand. Therefore, using only the newest machinery to dye the yarns is always recommended.
Only combed yarns are used for yarn dying. Additionally, the yarn needs to be stronger. Count Strength Product is the name of it (CSP)
Popular Yarn Formation Systems
After the cotton is removed from the bales, it is opened up, blended, and combined with cotton from other bales to create cotton yarn. The fibers are then shaped into a picker lap, a thin continuous web of interlaced fibers that are partially orientated. The picker lap is next put through carding to eliminate any remaining garbage and short fibers while giving the fibers more direction.
Before feeding to drawing, the cotton sliver from carded machines is combed to straighten further, orient the threads, and remove additional short tangled fibers. The drafting process is the name given to the part of the procedure that involves drawing.
The drafted, lightly twisted sliver (roving), fed from the drafting unit onto a high-speed spindle via a traveler holding the spun yarn to a ring enclosing the reciprocating spindle, is then drawn and high-speed twisted.
Woolen and Worsted Yarn Formation
To get rid of the contaminants, the wool is washed in a series of detergent baths. The procedure is known as scouring, and it has the potential to lower the weight of raw wool by as much as 50%.
By carbonizing the wool with concentrated sulfuric acid to liquefy the cellulose material, any leftover vegetable matter in the wool can be eliminated.
After washing and drying, the cleaned wool is mixed and carded to create a sliver. To be used in the worsted system, the sliver needs to go through extra straightening, orientation, and elimination of short strands. To give wool top, the procedure includes combing and gilling, which is a type of pin orientation. The wool top is drawn and slightly twisted in stages to create a roving, which is then spun into a worsted yarn with a lot of twists.
Other Staple Yarn Formation
The mill receives boxes of cut staple synthetic fibers prepared for carding and turning into yarn. It is essential to thoroughly blend two or more different staple fibers before carding and to double the sliver several times to ensure intimate blending before roving and spinning.
Filament Yarn Formation
Because the fibers are steady and do not need to be extensively twisted to produce a cohesive, strong yarn, filament spinning methods are far less complicated. Only the element of the ring spinning technique that involves twisting and winding onto spindles is used when spinning filament yarn, which often uses synthetic fibers.
Grindle/Twisted Yarns
These fibers are also referred to as “Twisted Yarns.” Twisted together are two yarns with the same counts but different hues. The brighter shade of one of these two hues will be present, while the deeper shade will be present in the other. The yarn will have a different mixing tint after twisting. We need to confirm that these yarns have the same counts and yarn strengths. Additionally, when they are twisted together, the yarn should have an even number of twists per inch (often 14). We will experience issues during knitting if the twisting is not done correctly.
Mercerised Yarn
The yarn will be signed after combing and twisting (gassed). (This is now referred to as Gassed Yarn.) the thread will be quickly burned during this procedure, and the nearby superficial hair will be removed. The yarn’s hairy particles will burn off as a result of increased heat.
The yarn is then subjected to an adequately controlled caustic soda treatment.
The yarn is then subjected to an adequately controlled caustic soda treatment. This procedure is known as merchandising. Mercerising is carried out to strengthen the yarn and enhance its sheen. (The yarn is now referred to as Gassed Mercerised Yarn.) the yarn will be extremely strong and brighter after mercerizing. Additionally, without getting wet, the yarn will absorb 20% more humidity. Additionally, this mercerizing process makes the yarn more resilient and slows down the accumulation of dirt.
Structure of a Yarn Formation Model
The mechanical behavior of fibers when bundled into yarn can be used to determine the quality of a model yarn. Even cellulose fibers have a mechanical body that is extremely long and flexible. With a breaking elongation lower than 10%.Sam Martin
Positions of the Fibers in Yarn Structure
Ring-spun yarn
The twist causes all or some of the fibers to adopt the necessary helical orientation. The spinning process has a significant impact on how many fibers are twisted and how much winding is applied.
Twisting happens from the outside inwards in ring spun yarns. Due to the larger degree of winding, the fibers have less inclination (angle between the fibers and the axis of the yarn) near the yarn’s periphery (the outer sheath A, see image 1) than at its center (the core B). Ring-spun yarn is referred described as having a “sheath twist” because the fibers gradually become less tightly coiled closer to the core.
The outer layers will typically take the axial forces when loaded. However, the radial pressures strengthen the axial resistance to the fibers separating by applying more pressure inward. In light of this, completely twisted yarns with “sheath twist” have high tensile strength but are less resistant to abrasion. The exterior, tightly wound fibers are broken down by abrasion. The strand loses cohesion because these fibers, which hold the yarn together, are broken.
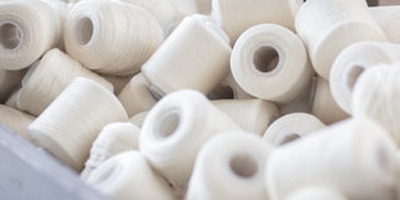
- Number of fibers in the cross-section
- Fiber disposition
- Fiber alignment
- Overall structure
- Twist